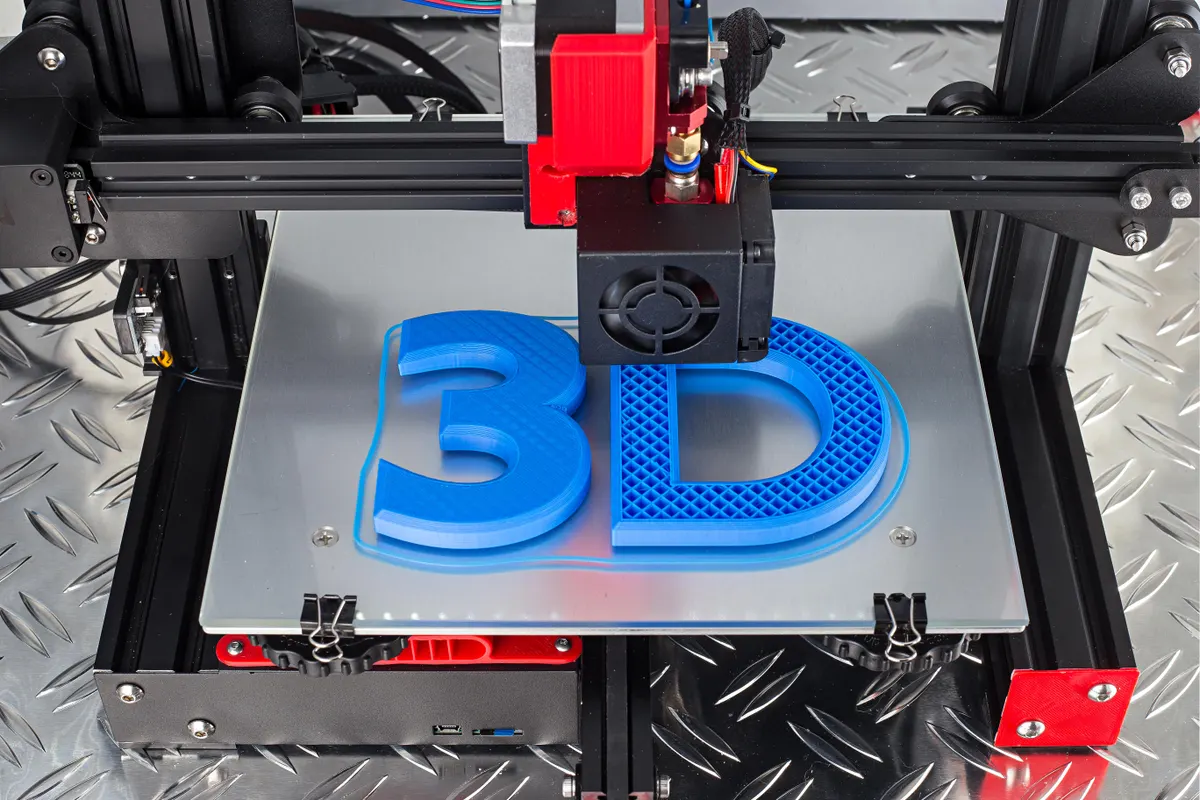
Design for Additive Manufacturing (DfAM) is a critical aspect of harnessing the full potential of 3D printing technology. Unlike traditional manufacturing methods, 3D printing allows for complex geometries, customization, and rapid prototyping. However, to fully capitalize on these advantages, designers and engineers must adapt their mindset and approach when creating designs for 3D printing. In this article, we will explore key considerations for successful DfAM, helping you unlock the true potential of 3D printing.
- Design Freedom and Complexity: One of the greatest strengths of 3D printing is its ability to create complex geometries that would be challenging or impossible to manufacture using traditional methods. Embrace this design freedom and push the boundaries of what is possible. Take advantage of the unique capabilities of 3D printing to create intricate internal structures, organic shapes, and lightweight designs. However, keep in mind the limitations of your chosen printing technology and materials to ensure printability and structural integrity.
- Optimization for Additive Manufacturing: When designing for 3D printing, it's essential to optimize the design for the specific additive manufacturing process and materials being used. Consider factors such as layer thickness, build orientation, support structures, and surface finish requirements. By understanding the capabilities and constraints of your chosen 3D printing technology, you can design parts that maximize performance, minimize material usage, and reduce post-processing efforts.
- Support Structures: Support structures are often necessary in 3D printing to provide stability during the printing process. However, they can be time-consuming to remove and may leave surface imperfections. Design with support structures in mind, strategically placing them where they are needed and minimizing their usage whenever possible. Consider incorporating self-supporting features, incorporating lattice structures, or utilizing soluble support materials to simplify post-processing.
- Material Selection: Different materials exhibit varying properties, such as strength, flexibility, and heat resistance. Understand the strengths and limitations of the materials available for 3D printing and choose the most suitable material for your specific application. Consider factors such as mechanical requirements, chemical compatibility, and aesthetic considerations when selecting materials. Conduct material testing and validation to ensure that the chosen material meets the desired performance criteria.
- Design for Assembly and Post-Processing: While 3D printing enables the creation of complex and fully assembled components in a single print, there may still be instances where post-processing or assembly is required. Design parts with ease of assembly and post-processing in mind. Incorporate features such as alignment pins, interlocking mechanisms, or snap-fit connections to simplify assembly. Consider the access required for post-processing steps like sanding, polishing, or painting, and design accordingly.
- Iterative Design and Testing: Take advantage of the rapid prototyping capabilities of 3D printing to iterate and test your designs. Embrace an iterative design process, allowing for quick design modifications and improvements based on test results and feedback. By rapidly iterating and testing, you can optimize your design for performance, functionality, and manufacturability, leading to better end products.
- Design for Scalability: Consider scalability when designing for additive manufacturing. If your design needs to be produced in larger quantities, ensure that it can be easily replicated and manufactured consistently. Think about design features that facilitate efficient printing, minimize material waste, and optimize production time.
- Collaboration and Knowledge Sharing: The field of 3D printing is constantly evolving, with new technologies, materials, and techniques emerging regularly. Stay updated with the latest advancements, collaborate with experts, and participate in knowledge-sharing communities. Engage with other designers, engineers, and manufacturers to learn from their experiences and gain insights into best practices for design for additive manufacturing.
Mastering design for additive manufacturing is crucial for unlocking the full potential of 3D printing technology. By considering key factors such as design freedom and complexity, optimization for additive manufacturing, support structures, material selection, design for assembly and post-processing, iterative design and testing, scalability, and collaboration, designers and engineers can create successful 3D printed designs.
Designers must embrace the unique capabilities of 3D printing to create complex geometries and lightweight structures that were once impractical or impossible to manufacture. By optimizing designs for specific additive manufacturing processes and materials, they can achieve optimal performance and reduce post-processing efforts. Careful consideration of support structures and their placement can streamline the printing process and improve the surface finish of the final part.
Material selection plays a crucial role in achieving desired mechanical properties and functional requirements. Understanding the characteristics of available materials and conducting material testing and validation are essential steps in the design process. Designing for ease of assembly and post-processing ensures smooth production and reduces overall manufacturing time.
The iterative design process, facilitated by rapid prototyping, allows designers to continuously refine and improve their designs based on testing and feedback. This approach leads to more optimized and successful end products. Additionally, scalability should be considered to ensure that designs can be efficiently produced in larger quantities.
Engaging in collaboration and knowledge sharing within the 3D printing community helps designers stay up-to-date with the latest advancements and best practices. Learning from the experiences of others and sharing insights can greatly enhance the design process and lead to innovative solutions.
As the field of additive manufacturing continues to advance, designers and engineers must adapt their mindset and approaches to fully exploit the possibilities offered by 3D printing technology. By mastering design for additive manufacturing, they can create successful and impactful 3D printed designs that drive innovation and unlock new possibilities across various industries.
Related Posts
Tree Services in Tigard: Protecting Your Property and Enhancing Your Yard
Trees play a crucial role in enhancing the beauty and value of your property. Ho...
Read More
The Evolution and Importance of Choir Chairs with Book Racks
In the world of music, particularly within choir settings, the comfort and funct...
Read More
Streamlining Construction Supplies: Where to Buy Concrete 200, Sand-Gravel Mix, and Crushed Stone in the Moscow Region
Efficient and reliable construction relies heavily on quality building materials...
Read More
Оптимизация Строительных Поставок: Где Купить Бетон 200, Пескогрунт и Щебень в Московской Области
Эффективное и надежное строительство невоз...
Read More